La industria farmacéutica enfrenta desafíos constantes en su búsqueda por garantizar la seguridad y la eficacia de sus productos. Una de las áreas más críticas en este ámbito es la de fabricación de medicamentos estériles, cuya normativa se ha visto recientemente modificada con la entrada en vigor del nuevo Anexo 1 en agosto del 2023. En este contexto, la implementación de Sistemas de Barrera de Acceso Restringido (RABS, por sus siglas en inglés) ha surgido como una de las principales alternativas para mejorar la seguridad y la calidad del proceso, en líneas de llenado ya existentes. Este artículo explora en profundidad la modificación de una línea de llenado convencional a un sistema RABS, abordando sus ventajas, desafíos y pasos clave para una transición exitosa.
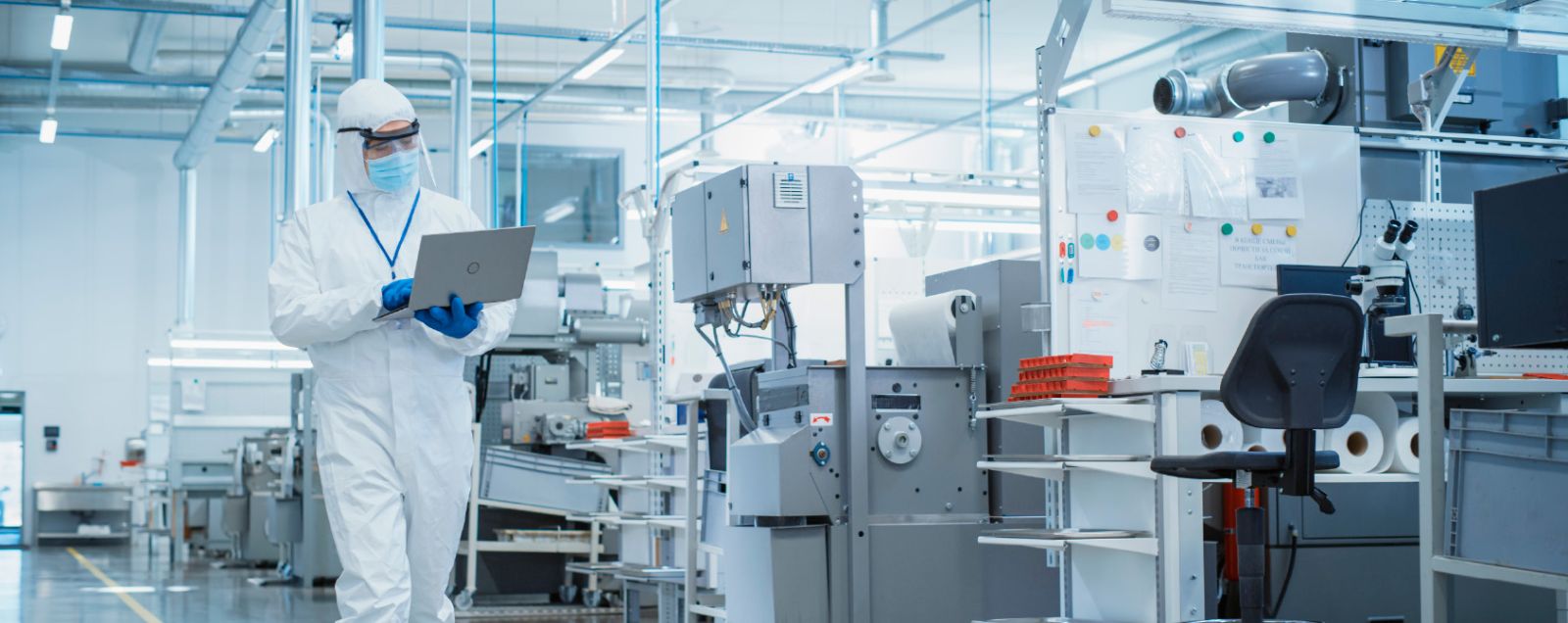
El llenado de productos farmacéuticos estériles es un proceso que debe cumplir con estrictas normativas de calidad y seguridad. La contaminación durante este proceso puede tener consecuencias graves, desde la ineficacia del producto hasta riesgos para la salud de los pacientes. Tradicionalmente, las líneas de llenado convencionales han sido utilizadas ampliamente, pero pueden presentar algunas limitaciones en términos de control de contaminantes. Los sistemas RABS representan una evolución tecnológica que proporciona una barrera física más estricta entre el ambiente, el operador y el producto, minimizando el riesgo de contaminación asociada con la intervención humana directa en las zonas críticas.
Con la entrada en vigor del nuevo Anexo 1 y la evaluación de riesgos para el control de la contaminación (CCS), en Inibsa nos plateamos la adaptación de una de nuestras líneas de llenado con esta tecnología.
¿Qué es un Sistema RABS? Ventajas y desafíos
Un Sistema de Barrera de Acceso Restringido (RABS) es una tecnología diseñada para proporcionar un entorno controlado durante el proceso de llenado farmacéutico. A diferencia de los sistemas de barrera convencional, que dependen en gran medida de la sala limpia para el control de contaminantes, los RABS crean una barrera física que separa el producto del operador y del ambiente externo. Existen varios tipos de RABS en función del nivel de aislamiento o separación que ofrecen: Open RABS (activos o pasivos) y Closed RABS.
En nuestro caso, y debido a las características y posibilidades de adaptación de nuestra línea actual, nos inclinamos por un sistema Active Open RABS.
La transición de una línea de llenado convencional a un sistema RABS ofrece múltiples ventajas, no solo a nivel de reducción del riesgo de contaminación, sino también a nivel de reducción de mermas y de optimización de los controles microbiológicos para monitorización del proceso. Por otro lado, en función de la tipología del medicamento, ofrecen una barrera adicional de protección para el producto y también para el operador, como es el caso de productos biológicos.
Sin embargo, el retrofit de una línea existente a un sistema RABS presenta ciertos desafíos que deben ser abordados adecuadamente, destacando:
- Costes Iniciales: La instalación de un sistema RABS requiere una inversión inicial significativa. Esto incluye no solo el coste del equipo y su instalación, sino también las modificaciones estructurales necesarias en la planta de producción.
- Coste de Oportunidad: El equipo afectado estará inoperativo por un período de tiempo significativo. En nuestro caso fueron 3 meses de línea completamente parada.
- Capacitación del Personal: La operación de un sistema RABS requiere una capacitación especializada del personal. Es fundamental que los operarios se formen en los nuevos procedimientos de set-up, operativa y limpieza del sistema para evitar errores que puedan comprometer la integridad del producto. Dentro del proyecto, se impartieron 3 semanas de formación teórico-práctica para cada turno de trabajo y se realizaron 3 APS con todo el personal destinado a esta línea de dosificado, lo que nos llevó 3 semanas más. Además, se construyó un nuevo Learning center (habilitado con una réplica de una línea de dosificado a escala real), que se utiliza tanto para formación inicial del personal como para la mejora continua.
- Mantenimiento y Validación: Los sistemas RABS requieren un mantenimiento riguroso y constante, especialmente en lo referente a la gestión de guantes y a su integridad, que requerirá de una pauta de testificación frecuente y acorde al análisis de riesgo realizado.
- Adecuación de toda la documentación relacionada: La actualización del equipo requerirá de la adecuación de toda la documentación del sistema de calidad impactada. En Inibsa, más de 60 documentos, entre los cuales procedimientos normalizados de trabajo, instrucciones, protocolos…fueron actualizados. Además, se emitieron 5 análisis de riesgos desde el punto de vista general, microbiológico, de intervenciones, de desinfección y validación de limpieza y del APS (Aseptic process simulation) que nos permitieron identificar y gestionar los principales impactos del cambio en la planta y en el proceso.
- Impacto en la eficiencia de la línea: La operativa del proceso mediante RABS puede tener un impacto en el OEE de la línea, tanto a nivel positivo por reducción de la merma, como a nivel negativo por incremento de los tiempos de limpieza y set-up.
Crónica de nuestro proyecto de transformación
Como ya se ha comentado, la transición de una línea de llenado convencional a un sistema RABS es un proceso complejo que implica varias etapas. En nuestro caso, el proyecto arrancó a finales de 2022.
La primera necesidad del proyecto fue el Diseño del sistema RABS, para ello se realizó un estudio de la ubicación de los puertos en la llenadora, de acuerdo con las necesidades de producción. Para una nueva línea, el estudio puede realizarse de forma virtual o bien mediante maqueta a escala real simulando las estaciones de la línea de llenado. Sin embargo, al tratarse de una línea existente, optamos por utilizar la propia máquina a la que le acoplamos un marco móvil con regulación en altura y que nos permitió realizar el estudio in situ.
Al utilizar nuestra propia máquina como maqueta, se pudieron simular intervenciones de rutina con el personal de la línea, tales como el set-up, asistencia durante el llenado, ajustes mecánicos, muestreos estáticos y dinámicos. Este estudio se realizó con un equipo de trabajo multidisciplinar que incluyó al proveedor del sistema, con una duración de 1 semana.
Además de definición de la ubicación de los puertos, el estudio permitió la identificación de sectores de aislamiento dentro del sistema RABS, en nuestro caso se identificaron 4 sectores: zona alimentación cartuchos de vidrio, zona de llenado, zona de capsulado y zona del conjunto filtrante. Desde junio 2023 a octubre 2023 se trabajó juntamente con los ingenieros del proyecto para congelar el diseño definitivo. Finalmente, el nuevo layout de máquina contaba con 7 sectores, 21 puertos RABS, 2 nuevas compuertas (pizza-door) y 2 pletinas para entrada y salida de placas de muestreo
A partir de esa fecha, en octubre 2023 empezó la fase de Modificación de la estructura, es decir, la construcción de marcos y puertas, además, el bloqueo de todas las puertas de la máquina requería un nuevo sistema de enclavamiento distinto al existente. Durante este período de 12 semanas, empezó también la fase de fabricación del sobre-stock (necesario para afrontar el paro de máquina previsto sin impactar a nuestros clientes).
En febrero 2024, empezaron los trabajos de Integración del equipo, empezando por la desinstalación de marcos y puertas actuales a la que siguió la instalación de los nuevos marcos, puertos y del sistema de barreras de seguridad. Estos trabajos duraron 1 semana, tras la cual vino la fase de reprogramación de la máquina e integración al dominio de Inibsa. Esta fase, seguida de la Validación de la línea (IQ/DQ/OQ), más la validación del equipo de integridad para los guantes, nos ocupó otras 4 semanas más.
Un proyecto que duró 18 meses, de los cuáles 8 meses desde la tramitación del pedido hasta la entrega del nuevo equipo RABS, y 14 semanas de línea fuera de uso por implementación del cambio.
Conclusión
La adopción de sistemas RABS está en constante crecimiento en la industria farmacéutica. La modificación de una línea de llenado convencional a un sistema RABS es una inversión estratégica que puede proporcionar beneficios significativos en términos de calidad, seguridad y cumplimiento regulatorio. Aunque la implementación de RABS presenta desafíos, estos pueden ser superados con una planificación adecuada, capacitación del personal y un enfoque integral en la validación y mantenimiento del sistema.
En nuestra experiencia, una estrecha colaboración con el proveedor es clave para el éxito del proyecto, puesto que la integración de los equipos es una fase crítica en la modificación de la línea de llenado. Esto incluye la instalación de la barrera física, los sistemas de ventilación y filtración, y los equipos de llenado automatizados.
La adopción de sistemas RABS representa un paso adelante en la evolución de la industria farmacéutica hacia estándares más altos de excelencia y responsabilidad. A medida que las normativas de calidad y seguridad se vuelven más estrictas, la necesidad de soluciones avanzadas como los RABS se vuelve más apremiante. Además, la evolución tecnológica está impulsando el desarrollo de sistemas RABS más eficientes y accesibles. En el futuro, se espera que los RABS se conviertan en el estándar de la industria, reemplazando gradualmente a las líneas de llenado convencionales.